Discover our capabilities and network
What Is Supply Chain Management (SCM)?
Supply chain management is the management of the flow of goods and services and includes all processes that transform raw materials into final products. It involves the active streamlining of a business’s supply-side activities to maximize customer value and gain a competitive advantage in the marketplace.
SCM represents an effort by suppliers to develop and implement supply chains that are as efficient and economical as possible. Supply chains cover everything from production to product development to the information systems needed to direct these undertakings.
Explaining Supply Chain Management (SCM)
How Supply Chain Management Works
Typically, SCM attempts to centrally control or link the production, shipment, and distribution of a product. By managing the supply chain, companies are able to cut excess costs and deliver products to the consumer faster. This is done by keeping tighter control of internal inventories, internal production, distribution, sales, and the inventories of company vendors.
SCM is based on the idea that nearly every product that comes to market results from the efforts of various organizations that make up a supply chain. Although supply chains have existed for ages, most companies have only recently paid attention to them as a value-add to their operations.
In SCM, the supply chain manager coordinates the logistics of all aspects of the supply chain which consists of five parts:
- The plan or strategy
- The source (of raw materials or services)
- Manufacturing (focused on productivity and efficiency)
- Delivery and logistics
- The return system (for defective or unwanted products)
The supply chain manager tries to minimize shortages and keep costs down. The job is not only about logistics and purchasing inventory. According to Salary.com, supply chain managers, “make recommendations to improve productivity, quality, and efficiency of operations.”
Improvements in productivity and efficiency go straight to the bottom line of a company and have a real and lasting impact. Good supply chain management keeps companies out of the headlines and away from expensive recalls and lawsuits.
Supply Chains
A supply chain is the connected network of individuals, organizations, resources, activities, and technologies involved in the manufacture and sale of a product or service. A supply chain starts with the delivery of raw materials from a supplier to a manufacturer and ends with the delivery of the finished product or service to the end consumer.
SCM oversees each touchpoint of a company’s product or service, from initial creation to the final sale. With so many places along the supply chain that can add value through efficiencies or lose value through increased expenses, proper SCM can increase revenues, decrease costs, and impact a company’s bottom line.
Example of SCM
Understanding the importance of SCM to its business, Walgreens Boots Alliance Inc. placed focused effort on transforming its supply chain in 2016. The company operates one of the largest pharmacy chains in the United States and needs to efficiently manage and revise its supply chain so it stays ahead of the changing trends and continues to add value to its bottom line.
As of July 5, 2016, Walgreens has invested in the technology portion of its supply chain. It implemented a forward-looking SCM that synthesizes relevant data and uses analytics to forecast customer purchase behavior, and then it works its way back up the supply chain to meet that expected demand.
For example, the company can anticipate flu patterns, which allow it to accurately forecast needed inventory for over-the-counter flu remedies, creating an efficient supply chain with little waste. Using this SCM, the company can reduce excess inventory and all of the inventories’ associated costs, such as the cost of warehousing and transportation.
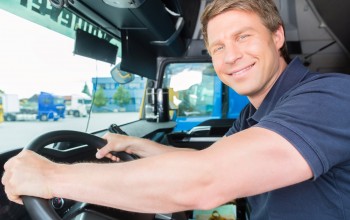
Prime Auto Routes GmbH in Asia Pacific
- Operating in all major countries and borders
- Extensive services including: linehaul, Pick Up and Delivery (PUD), home delivery, milkrun, cross-border, courier and rail
- Singapore to Shanghai cross-border service
- China to Europe railway service: Innovative service balancing speed and cost; faster than Oceanfreight, cheaper than Airfreight
- Linehaul China: 700 trucks a day, 6.25 million pallets moved yearly
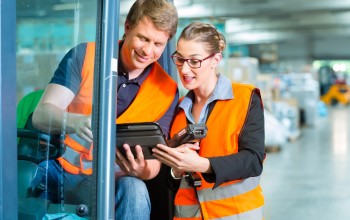
Transportation across Europe
- Multi-sector and multi-mode capabilities
- Working with Pan-European players and niche specialists
- Central control and network monitoring through the Control Tower
- 450,000 tons managed a year
- 40,000 shipments a year
- 200 transport partners
- Groupage/LTL/FTL
- In Turkey, Logistics handles over 7,700 FTL trips a month
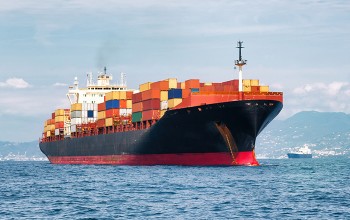
Prime Auto Routes GmbH in North America
- Supports U.S. Domestic network through LTL/FTL services
- Over 70,000 scheduled linehaul segments per year
- Seven hubs and 62 stations
- 7.5 million miles a month
- 8,000 loads a month
To learn more about our ground transportation operations in North America and how we can support your business, please visit our Home Page
Combining transport execution and transport management services
Through our global network of control towers and state-of-the-art technology, we are able to monitor and dynamically react to situations such as adverse weather, additional pick ups or drop offs, or heavy traffic, meaning that your goods are always travelling the most efficient route.
Our non-asset based Road network provides you with flexibility, improved service levels, accelerated delivery, reduced direct and indirect costs and much less
Frequently Asked Questions
Still open questions?
The Buyer’s payment will not be released to the Seller until the Buyer has accepted the vehicle, eliminating the concern for non-shipment or delivery. In the event that the Buyer has paid funds into Prime Auto Routes GmbH and the Seller does not ship or deliver the cargo, the Buyer may request Prime Auto Routes GmbH to start the 48 hour cancellation period. At the conclusion of the cancellation period, the payment is returned to the Buyer less all Prime Auto Routes GmbH fees.
Payment for vehicle transport service must be made in advance by Bank Wire Transfer. Bank Wire Transfer offers security as both parties (sender & recipient) must be identified by the bank.
The Buyer is notified by Prime Auto Routes GmbH that the merchandise is in their custody. When merchandise arrive in custody of Prime Auto Routes GmbH, transaction started.
If the Buyer rejects the merchandise, the Seller is required to pay for return shipping fees.
The Inspection Period is the specified amount of time agreed upon by both parties in which the Buyer may examine the merchandise/domain(s) after receipt. The time frame selected for the Buyer can range between 1 to 30 days and must be agreed upon by all parties at the beginning of the transaction. The Inspection Period begins when the Buyer marks the merchandise as received, or Prime Auto Routes GmbH verifies or receives confirmation that the merchandise has been delivered. The Buyer must accept or reject the goods within this period. If the Buyer has rejected and returned the merchandise, the Seller will be provided with a five day inspection period to examine the returned merchandise.
You benefit from our experience in delivering effective solutions to the complex global supply chains of some of the world’s biggest corporations.
You benefit from every innovation, whether it involves a simple extension to our Air and Ocean Freight products, whether it means a development in warehousing.
All of which explains why you’ll find the team of outstanding support at Prime Auto Routes GmbH ready to apply their passion for solutions in support of your business.